Energy-saving techniques for heat treatment in tube furnace
Time:2020-08-18 13:48
Heat treatment furnace is a general term for industrial gas furnaces for heat treatment of various metals on metal workpieces. The tube furnace heat treatment has brought great contributions to our production, life and economic development. The heat treatment furnace has many ways to save energy in the usual production process and use. So how does the gas heat treatment furnace achieve energy saving? Now let's reveal four tips for energy saving in heat treatment furnace!
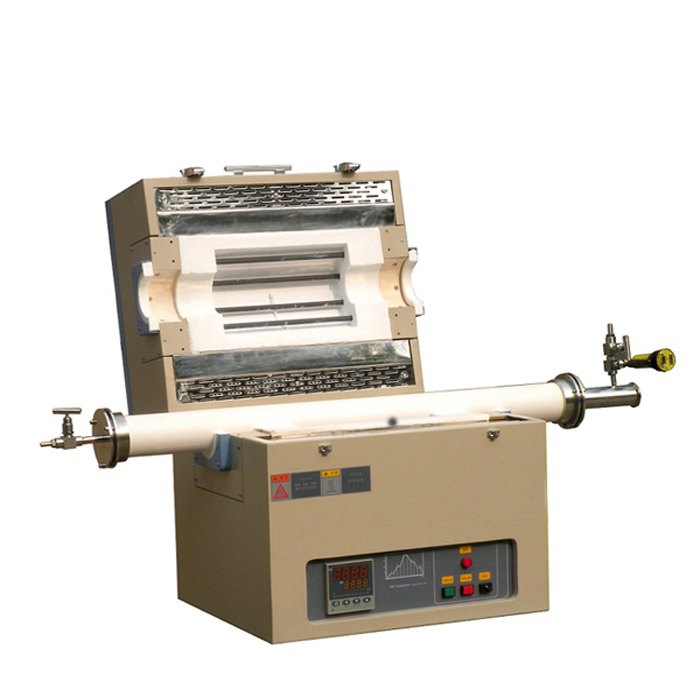
1. Heat treatment furnace equipment maintenance and maintenance: The equipment should be regularly repaired during production, and the furnace and furnace door should be checked for airtightness. The related instruments and meters of the distribution box should be calibrated and maintained regularly to reduce the loss caused by the shutdown of the furnace due to electrical failure. The maintenance of related operating equipment such as trolleys and traveling vehicles reduces the loss caused by the inconvenience of entering and exiting the furnace.
2. Cooling medium of heat treatment furnace: Many mechanical parts of tube furnace heat treatment are alloy structural steels, and aqueous quenching prevents large-diameter, medium-carbon and low-alloy steels that may not reach the oil quenching hardness value for heat treatment, and water quenching is easy to crack. , Water-soluble synthetic quenching fluid is especially suitable for low and medium carbon steel induction and large-piece quenching. Water-soluble synthetic quenching fluid is especially suitable for low and medium carbon steel induction and large-piece quenching. By adjusting the concentration, the rotary kiln can obtain different Cooling speed, the quenched workpiece is bright and has a short-term anti-rust effect, and it can be tempered directly without cleaning, and there is no soot. No oily smoke, no burning, no fire hazard, improving the working environment. It is not easy to age, deteriorate, and has a long service life, compared to oil products. The cost is relatively small.
3. The tempering process of the heat treatment furnace: the tempering process is to determine the waste heat of the heat treatment furnace to be used according to the tempering temperature of the parts. The general rule is that the tempering temperature of the parts is lower than the furnace waste heat temperature by about 300 degrees, in which case the workpiece is subjected to heat treatment After the furnace, the furnace quickly reaches the set temperature of the tempering process, and there are multiple temperings that are better than one tempering. Therefore, in mass production, the structure and performance of the secondary tempering is better than that of the one tempering, and the cost is correspondingly reduced. .
4. Control of the quality of the heat treatment furnace: In fact, when the workpiece is heat treated, it is itself energy-saving. If a workpiece is not subjected to effective and reasonable heat treatment, the use time limit of the part will not be very long, and the early failure of the part must be manufactured Replace with new parts, which will have to clean up raw materials, machining man-hours, and other related expenses. Effective and reasonable heat treatment can double the service life of the workpiece. Therefore, good heat treatment quality can avoid the early failure of the workpiece, and can avoid a series of procedures such as normalizing, re-quenching and tempering, correction, stress relief and tempering.
HOT PRODUCTS
-
High temperature box resistance furnace
-
PT-V1700 graphite vacuum furnace
-
RTP Tube Furnace
-
Feeding and discharging rotary tubular furnace